Tumbling / Mechanical polishing / Electropolishing / Anodized / Hard Anodized / Zinc plating / Nickel Plating / Electroless Nickel Plating (EN Plating) / Black Oxide / Electro-deposited Coating (ED Coating) / Liquid coating / Powder coating / Chrome Plating / Gold Plating / Silver Plating / Tin Plating / Hear treatment / Case harden
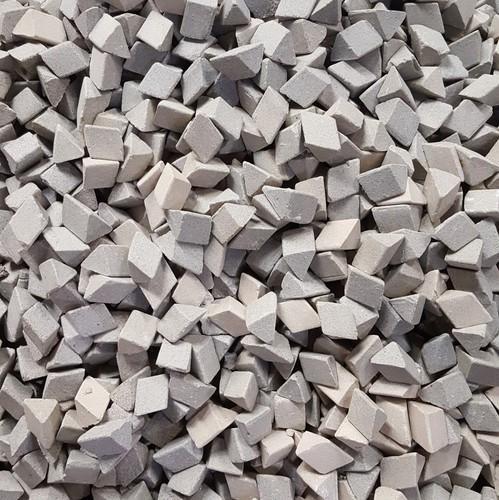
Tumbling (Vibration grinding)
Tumbling is a step of deburring and removing the edge. Proper grinding removes the damaged or deformed surface of the material while limiting the amount of additional surface deformation. The goal is to make the surface smooth with minimal damage in the shortest possible time.
Tumbling removes burrs by using abrasive particles. There are different shapes and materials of abrasive particles that can be used based on the products of material and surface roughness requirement. The tumbling process with suitable abrasive grains can produce the lowest amount of deformation while providing the highest removal rate.
Mechanical polishing
Polishing is used to remove the damage remaining from the grinding process to make the surface quality like mirror gloss. The surface roughness is under Ra0.2. This is achieved by successive steps with finer abrasive particles and tools.
Electropolishing
Electropolishing is a chemical surface-finishing technique. The metal burrs or machining marks can be electrolytically removed from the surface. The primary purpose is to minimize the surface roughness, thus greatly reducing the risk of dirt or residues adhering and improving the cleanability of surfaces.
Electropolishing has become a common treatment for stainless steel in industries in which corrosion-resistance and cleanability requirements are particularly high. Typical applications are found in the pharmaceutical, biochemical and food-processing industries.
Since electropolishing doesn’t involve mechanical, thermal, or chemical impact, small and mechanically fragile parts can be treated. Electropolishing can be applied to parts of almost any shape or size.
Anodized
Anodizing (Type II) is an electroplating method of a metal part (mostly aluminum part) by forming a layer of oxide on its surface. It increases resistance to corrosion and wear, and provides better adhesion for paint primers (like screen printing) and glues than bare metal does.
The commonly used colors are nature (clear) and black. If any requirement about special colors, pls provide color samples for our production reference. Besides, Gloss difference is also divided into two types: bright(glossy) and matte.

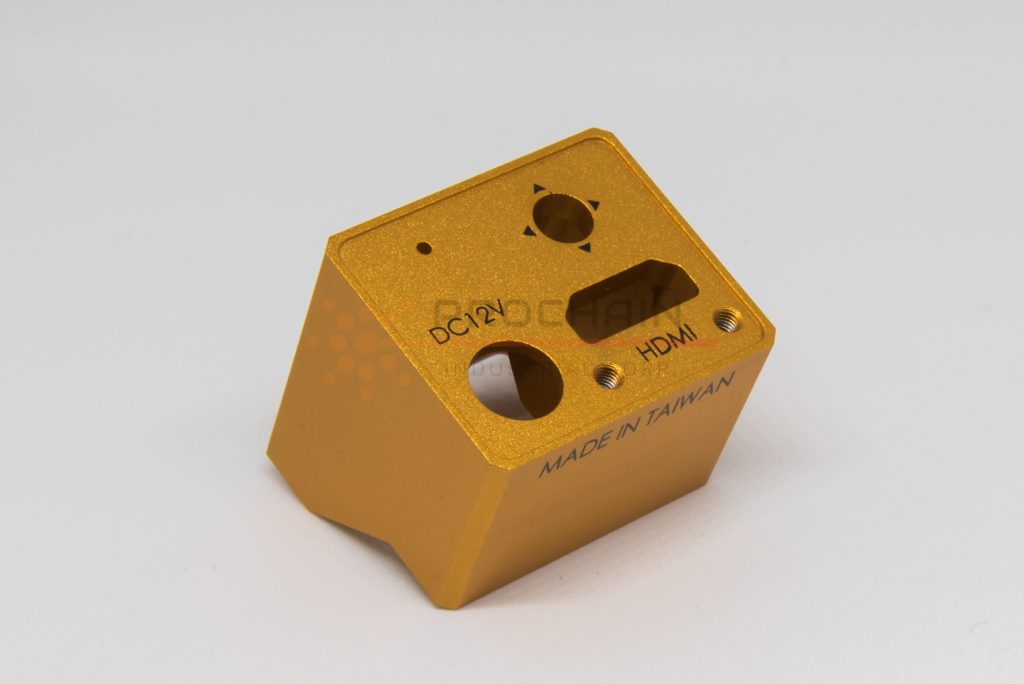
Hard Anodized
Hard anodized, sometimes called Type III, offers greater corrosion protection and resistance to wear in extreme environments or frequent use. This is produced by continuing the electrical current until the depth exceeds 20 microns or even more. This takes more time and is more expensive but produces a superior result.
Zinc plating
Zinc plating is typically used for screws and other fasteners, automotive parts, and various small parts that will be exposed in interior or mildly corrosive conditions. When a zinc coating is electroplated onto the surface of metals, it creates a formidable corrosion-resistant barrier.
For RoHS and REACH compliance, the specification ASTM B633 with trivalent chromate (Cr3+) conversion coating is commonly used. In addition, there are many different colors of zinc plating like white, blue, black, and yellow. The main purpose is to prevent corrosion and provide aesthetic functions.
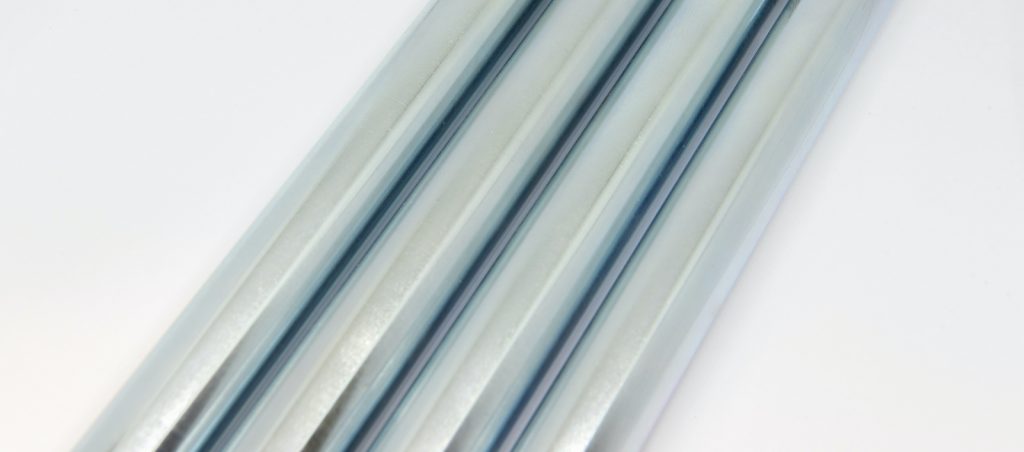
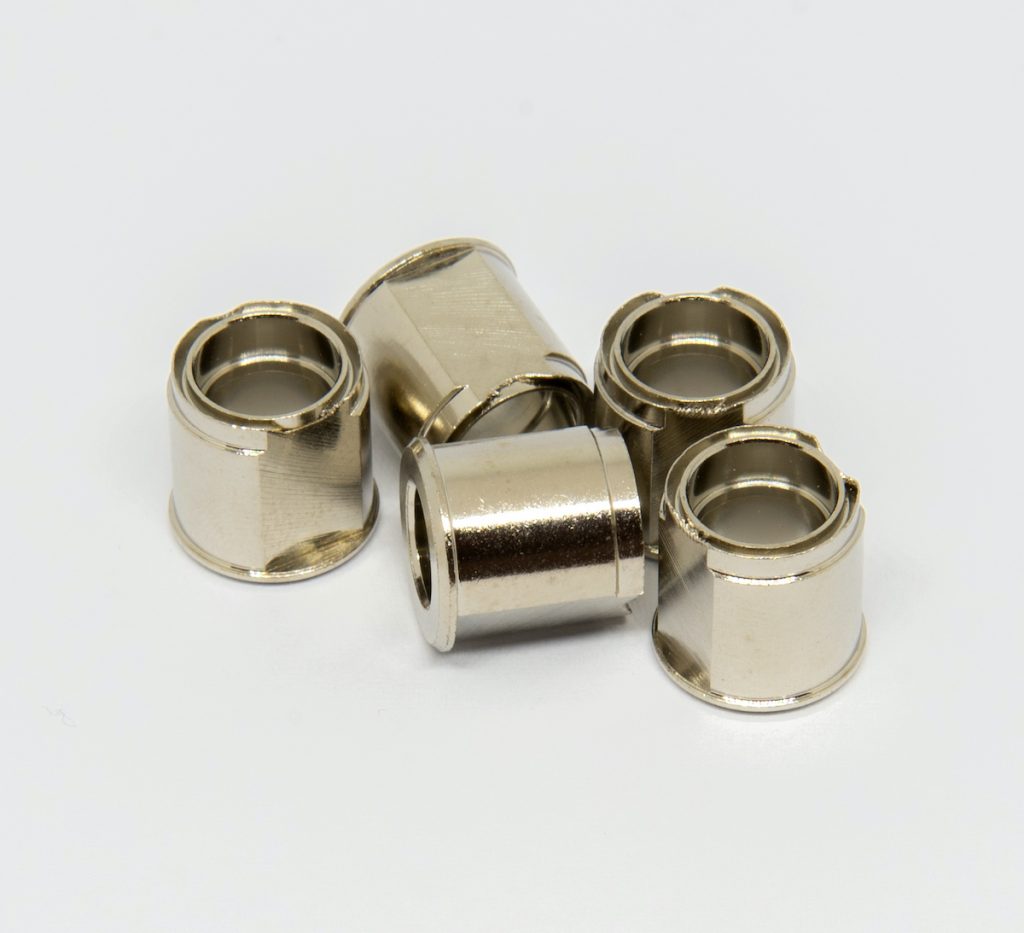
Nickel Plating
Electroless Nickel Plating (EN Plating)
Electroless nickel plating is a technique of electroplating a thin layer of nickel onto a metal object. It is also known as autocatalytic or chemical nickel plating. The general plating problems like edge build-up, uneven plating, and partial plating are not common with electroless nickel plating. In contrast to general nickel plating, the cost will be higher but the surface quality is better and more stable.
In addition, electroless nickel plating is also extended used in the manufacture of printed circuit boards (PCBs), like electroless nickel immersion gold (ENIG).
Black Oxide

Electro-deposited Coating (ED Coating)
The purpose of electro-deposited coating (ED coating) is to improve the anti-rust ability. It could form a strong film through electrophoresis, and strengthen the anti-corrosion ability of the workpiece. The commonly used color is black.
The biggest advantage is that the film thickness is uniform and smooth. Besides, the paint can cover the complex parts and objects, including the inner side and the surface, which can effectively prevent rust. The weakness is that the film thickness is relatively thin and easier to wear. If the requirement is a thicker coating, It is recommended to use powder coating or liquid coating.
Liquid coating
Powder coating
The pre-treatment of powder coating is basically the same as the liquid coating. The surface of the sprayed object must be clean, free of oil and dust, and then doing chemical pre-treatment such as chem film (alodine) to make the surface increases the corrosion resistance and adhesion of the coating film.
The characteristic of powder coating is in powder form. It does not need to be diluted and does not contain solvent and liquid components. The electrostatic spray gun allows the coating to be electrostatically charged and adhere to the surface of the object. The liquefaction of the coating is achieved by heating and melting. The baking temperature is at least 200°C.